Flow Metering 101: A Guide to Measuring Flow
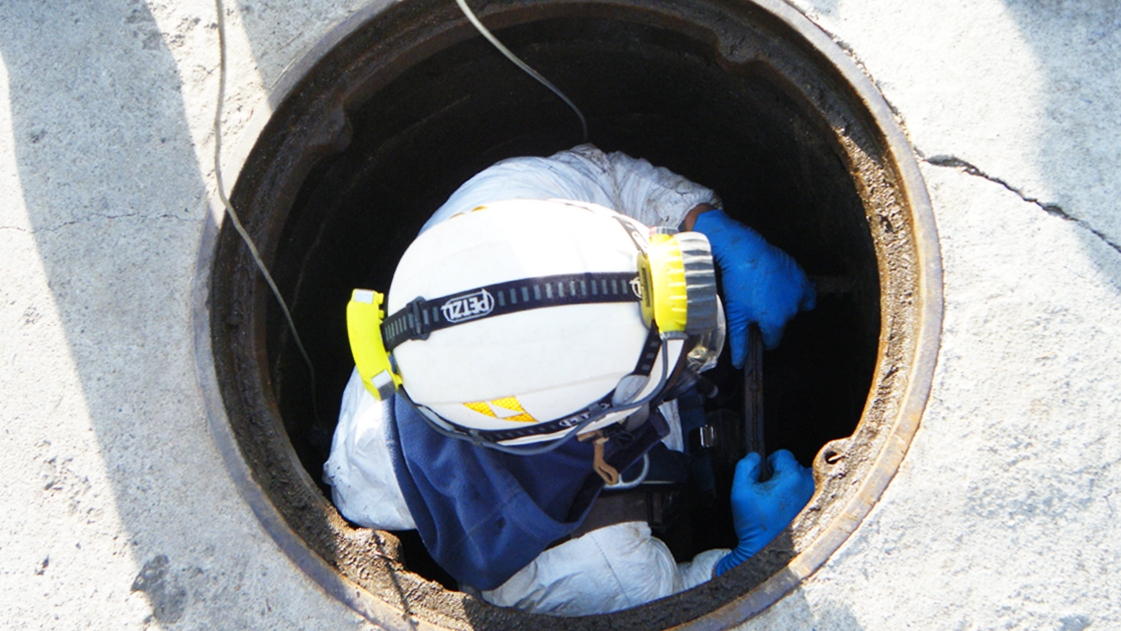
Introduction
Flow is the volume of fluid that passes in a unit of time. In water resources, flow is often measured in units of cubic feet per second (cfs), cubic meters per second (cms), gallons per minute (gpm), or other various units. Measurement of flow in water resources is important for applications such as system control, billing, design, and many other applications. There are several methods to measure flows in water resources systems. This article outlines a few of the more common flow metering methods and provides some background information on flow measurement.
Continuity Equation for Flow
For water flowing in a pipe under steady-state conditions (i.e., not changing over time), continuity means the water that flows into one end of a pipe must flow out of the other end. This also means that the flow rate in the pipe is the same at any location along the length of the pipe. The continuity equation can be represented as:
Flow = velocity * area
The notion of continuity under steady state conditions results in the product of the velocity * area being equal to a constant at any location along the pipe. This is a useful principle for making flow measurements, as will be demonstrated below.
Here is an example of a computation of flow using the continuity equation. The velocity is measured as 10 feet per second and the cross sectional area of the flow is measured as 10 square feet. Flow = 10 feet per second * 10 square feet = 100 cubic feet per second.
Common Flow Metering Methods in Open Channels
Eyeball Method
Sometimes it is useful to estimate flow using your eyes to estimate the velocity and cross sectional area, and then multiplying the velocity times the area to get flow (continuity equation). A ruler or tape measure can be used to improve the accuracy of the cross sectional area measurement, and a stopwatch can be used to improve the velocity measurement by timing a floating piece of debris traveling a set distance. The eyeball method can useful to estimate flow when the “order of magnitude” of the flow is all that is needed, or when the flow is so low that it is not possible to measure with a flow meter.
Depth to Flow (Manning’s)
It is possible to compute flow using the Manning Equation by making a measurement of the depth only, when the channel cross sectional area and channel slope are known and there are uniform flow conditions. The Manning’s equation is an empirical formula that describes the relationship between the velocity and the depth, slope and channel friction coefficient (Manning’s n) in an open channel under uniform flow conditions. Uniform flow means that the depth does not change over the length of the conduit or channel. Using the Manning equation for flow from a depth measurement is not applicable under gradually varying flow conditions such as backwater conditions upstream of a dam or weir.
The depth to flow method for flow measurement is more accurate than the “eyeball method.” The main challenges with flow measurement by depth only are inaccuracies in the estimate of the Manning’s n, the cross sectional area, and the potential for non-uniform flow conditions. This method is often used at USGS stream gauges to estimate the flow of a river by measuring only the stage of the river. Often in these causes, the stage/discharge relationship of the river was developed with the assistance of a complex hydraulic model of the river to account for complex channel geometries and channel friction conditions.
Primary Device
A primary device is used to measure open channel flow using a structure like a flume, weir or dam that enables the measurement of flow by measuring the depth. An equation or rating curve equation can then be used to convert the measured depth to a flow rate.
Primary devices work by forcing the flow to path through critical depth, such as at the crest of a weir or in the throat of a flume. In technical terms, critical depth is defined as the depth that results in the minimum specific energy state for a particular discharge. In practical terms, this energy-minimum state means that there is only a single flow rate that corresponds to the critical depth. Therefore, measuring only the depth yields a measurement of the corresponding flow, hence the term “primary” device.
Primary devices are a very convenient way to measure flow because the depth can be measured from above the flow without having to insert a sensor in the water. This makes primary flow meters more reliable and easier to maintain. One disadvantage of primary devices is that the can cause head loss and backwater in the system. Primary devices are generally considered the most accurate way to measure flow in open channels.
Area-Velocity Meter
An area-velocity meter is an open channel flow meter that measures flow by making two separate measurements of depth and velocity. The depth is converted to cross sectional area using the geometry of the pipe or channel. The flow is then computed using the continuity equation by multiplying the flow area times the velocity, hence the name “A-V meter.” The velocity is often measured using a Doppler sensor that bounces ultrasonic waves off particles in the fluid and uses the Doppler shift in the reflected sound signal to estimate the velocity. Some A-V meters measure the surface velocity optically to estimate the velocity. Some common A-V meter manufacturers include ISCO, ADS and Hach who makes Sigma and Marsh-McBirney meters.
A-V meters are commonly used to measure open channel flow in sanitary sewers, because the probes are relatively small and they can be installed in an existing sewer pipe without causing significant head loss in the pipe. This also makes them useful for temporary or short-term flow metering applications for sewer studies. A disadvantage of A-V meters is that the sensor must be installed in the fluid. In sanitary sewers, this necessitates frequent maintenance to clean the sensors. A-V meters are generally considered less accurate than primary flow meters, because a primary device only has to measure depth, and the measurement of depth is more accurate that then measure of velocity.
Transit Time Meter
Transit time meters were developed in the petroleum industry for accurately measuring flow in large pipes. They have been adopted to use in open channel flow for water metering applications with some success. Transit time meters also use ultrasonic waves like a Doppler meter, but instead of bouncing the sound waves off particles in the water like a Doppler meter, transmit time meters send the ultrasonic wave between two sensors located some distance apart from each other along the length of the pipe, and use the transmit time of the sound waves to compute the water velocity. Because the speed of the sound in water is known, the water velocity can be computed from the shift in the ultrasonic transit time that occurs due to the velocity of the water.
Transmit time meters can be expensive relative to Doppler flow meters because of the many sensors involved and the complex installation. They can be more accurate due to the ability to slice the flow into horizontal cross sections and measure velocity across each section.
Common Flow Metering Methods in Full Pipe Applications
Venturi Meter
A Venturi meter measures flow in full or pressure pipes using the Venturi effect by using a converging section of pipe to constrict the flow. Following the continuity equation, the converging section has a smaller cross sectional area, and therefore a higher velocity in the throat. This higher velocity in the throat results in a pressure drop in the throat, thanks to the conservation of energy and the Bernoulli Principle. Flow can then be determined by measuring the pressure drop in the converging section and using the Bernoulli equation to compute the flow. Venturi meters are more common in water metering applications, because the pressure measurement ports can become clogged in wastewater application.
Turbine Flow Meters
Turbine flow meters are a mechanical flow meter that makes use of a rotating turbine in the flow stream to measure the flow of water in the pipe. The rotational speed of the turbine is proportional to the velocity and flow can then be computed using the continuity equation. Turbine meters are used only in water applications due to the potential issues of wastewater solids collecting and clogging the turbine.
Magnetic Flow Meter
Magnetic flow meters work by applying a magnetic field to the flow passing through the pipe. This induces a small electronic potential difference (thanks to Faraday’s law and electromagnetic induction) that can be measured by electrode sensors. The magnitude of the electronic potential difference is proportional to the velocity of the water, and flow can then be computed using the continuity equation.
One advantage of magnetic meters is that the metering section is the same diameter as the adjacent pipe, so a magnetic meter causes no additional head loss. Most often magnetic meters are used in full (pressure) pipe applications, but open-channel magnetic meters are now available as well.
Conclusions
There are many ways to measure flow. Each method has various advantages, disadvantages and accuracies in different applications.
It is important to understand the characteristics of the various flow measurement techniques to help select an appropriate flow metering type for your application, or to properly interpret the flow measurements from an existing meter. A tool like H2Ometrics—a cloud-based water data analytics company—is helpful to examine the measurements collected by a flow meter and performs diagnostics to understand the meter performance and quickly process and analyze the data.